I needed a lightweight, impact resistant, streamlined fairing for a flying robot. I could 3d print a part with the right shape, but 3d printed materials would either be too weak, or too heavy. I’ve been considering a hybrid workflow which this was the perfect opportunity to try out: 3d printing a mold for composite layup.
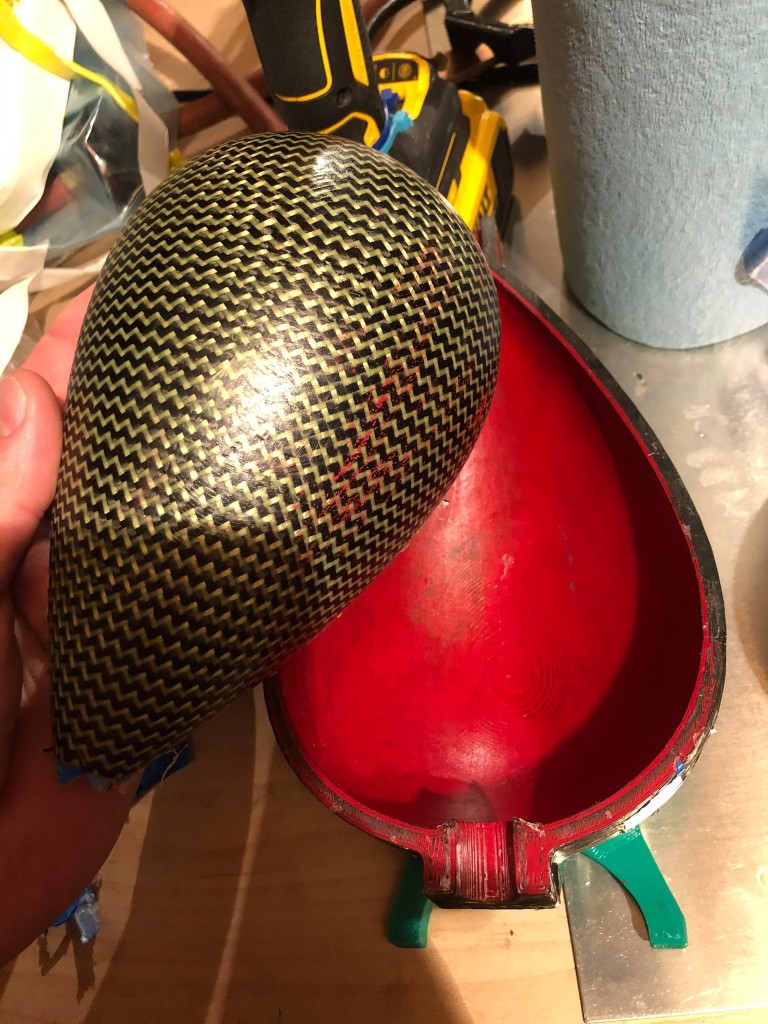
It worked wonderfully! The mold printed overnight, and after some sanding primer was applied and sanded down to a 600 grit finish, I waxed the mold, and it was ready to invest with fabric. I vacuum bagged the parts for good consolidation, and am very pleased with the results, shown above.
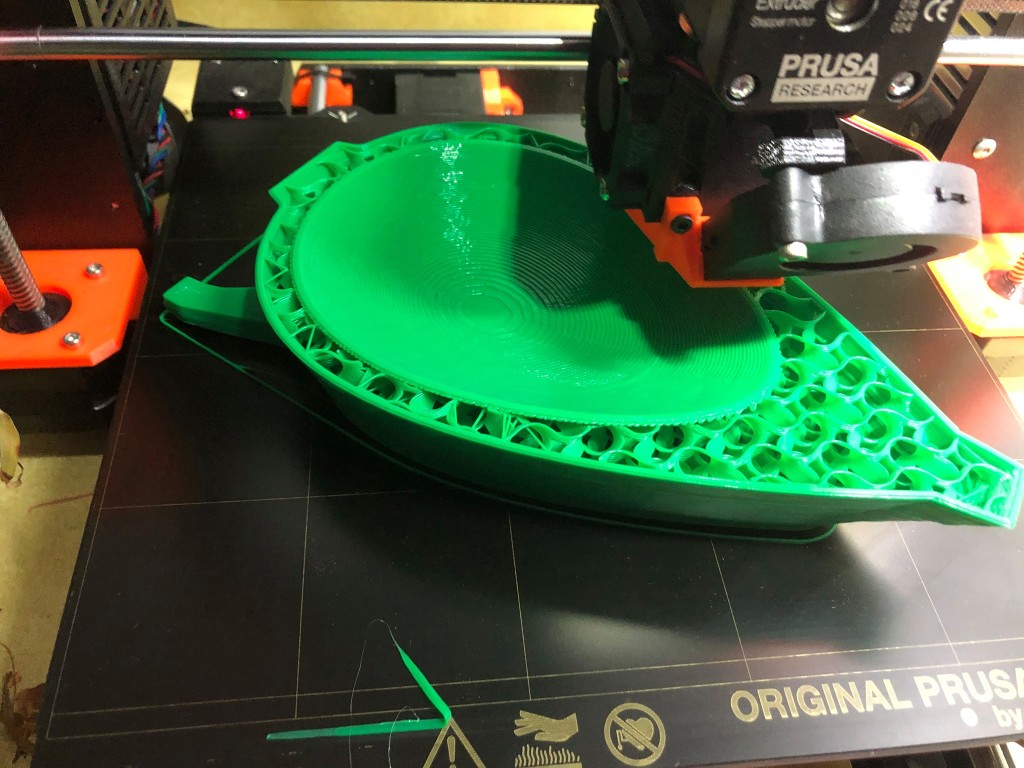
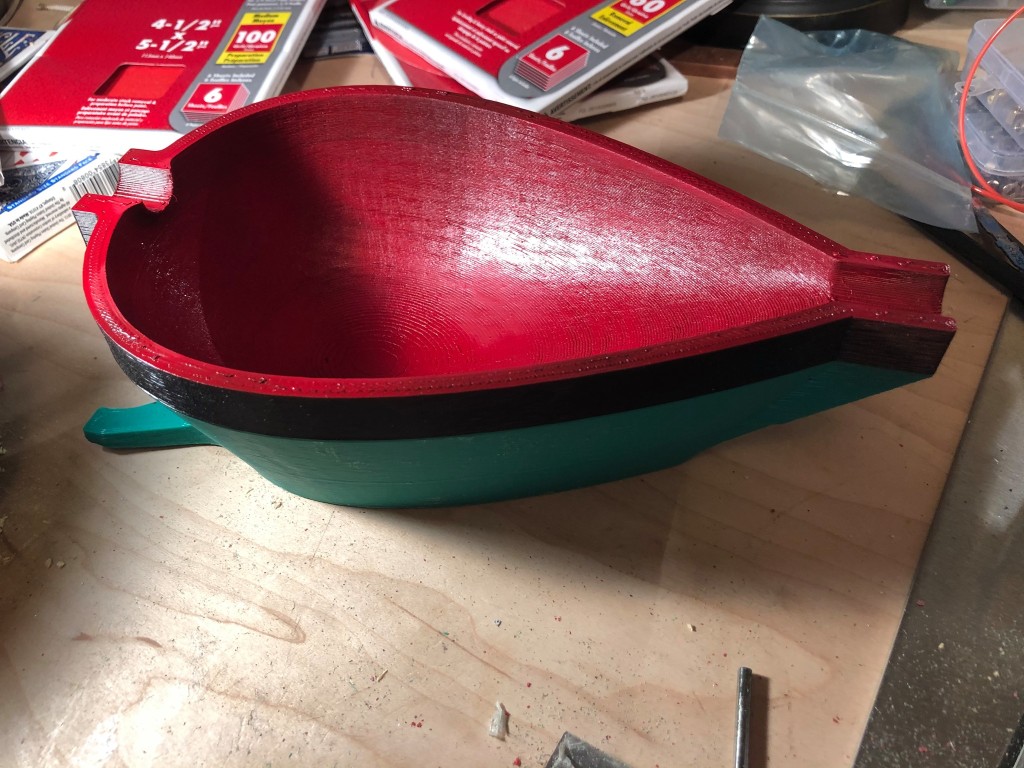